Production of aluminium
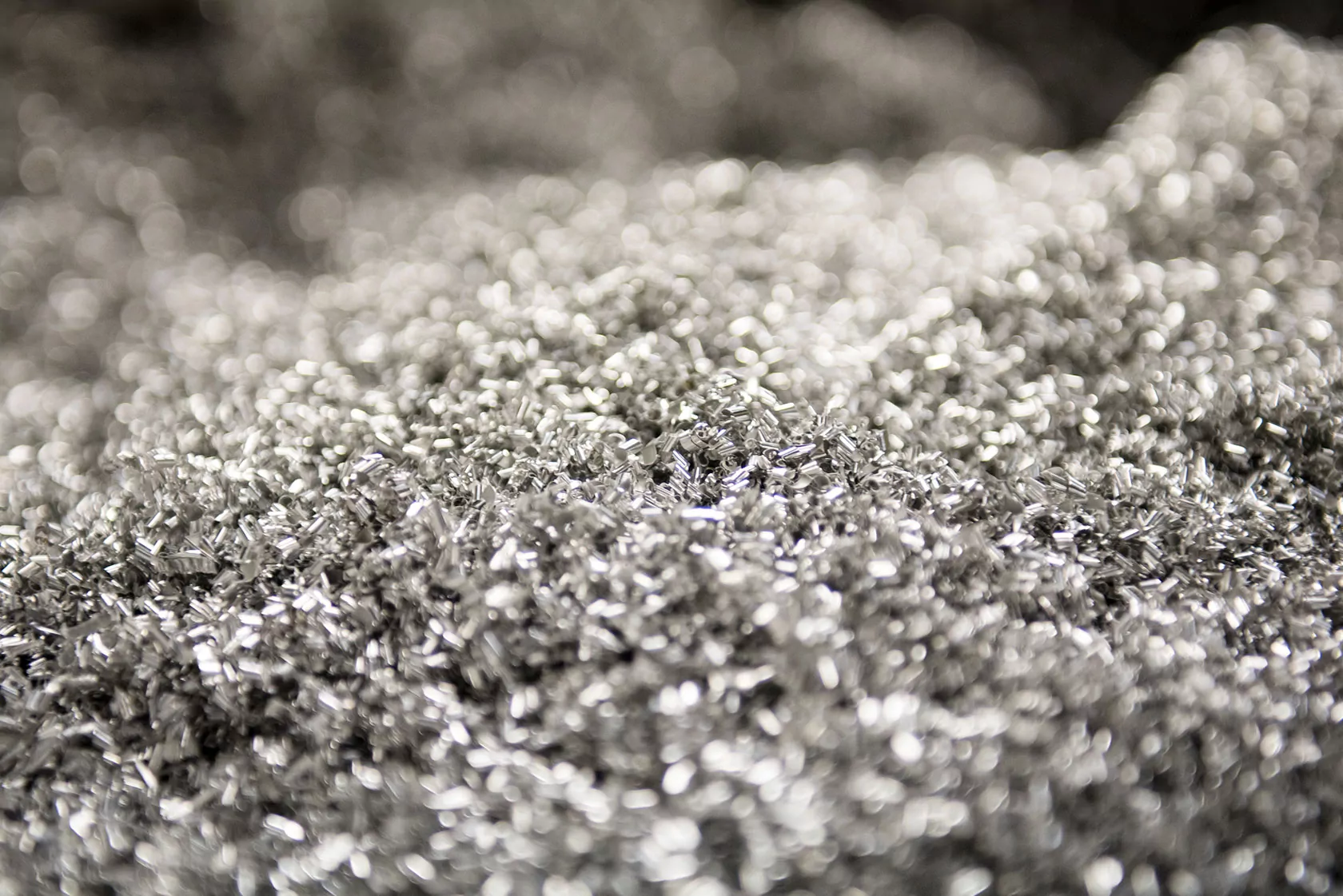
Aluminum is produced from the raw material bauxite. The bauxite is crushed and ground into a powder from which aluminum oxide is then extracted using lye and lime. Through melt electrolysis, primary aluminum can then be produced which is allowed to solidify into billets or ingots.
Aluminum undergoes various processes to become a finished product. This can be, for example, rolling to make sheet metal, casting to create the desired shapes, or extrusion to create profiles and bars.
During the process, different types of alloying elements are usually added to give the aluminum specific properties that are suitable for the intended area of use. Examples of such additives are silicon and magnesium. Here you can read more about aluminum alloys.
Aluminum is produced from the raw material bauxite
Bauxite is a commodity and sedimentary rock that consists of 50–65% alumina, which corresponds to 25–30% pure aluminum. The bauxite consists of a mixture of several minerals and is usually reddish-brown in color and similar to clay. The rock often occurs 5–10 meters below ground level and is mined in large parts of the world, with Australia accounting for the largest occurrence. Its primary use is for the production of aluminum. In Sweden, however, there is no bauxite deposit and overall there is limited mining of bauxite within the EU.
Bauxite and environmental impact
Bauxite has a high melting point and therefore large amounts of energy are required in the production of aluminium. Mining also has an impact on the environment and can be negative for the area where it takes place if the mining is not carried out correctly. However, aluminum can be recycled without losing its properties, and much of the aluminum ever produced is still in use today.
At Interal, we manage this by carefully sorting the scrap fractions that arise during processing. Cutting waste and processing chips are sorted and disposed of so that it can be melted down and used again without losing any of the material.
Read more about aluminum recycling.
Aluminum extrusion
Extrusion of aluminum is a manufacturing process where aluminum billets are shaped into the desired type of profile by extrusion.
The aluminum billet is heated to a temperature of between 450-550 degrees Celsius and then pressed through a tool (matrix) which consists of one or two parts depending on whether it is to be a solid or hollow profile. The aluminum profile is then cooled with air or water, stretched to release any tension in the material, and then proceeds to hot or cold aging which gives the material its final strength.
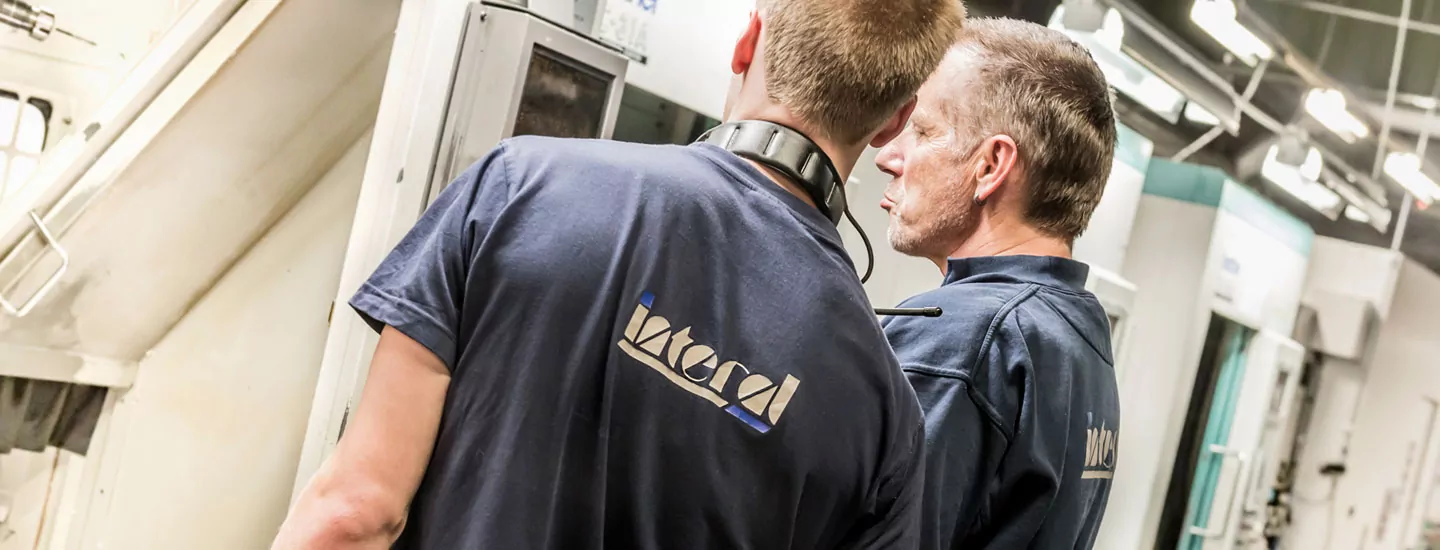
Do you have questions about aluminum manufacturing or our products?
At Interal, we have extensive knowledge of aluminum manufacturing and broad technical expertise. Contact us and we will tell you more about our services, products, and how we can help you!